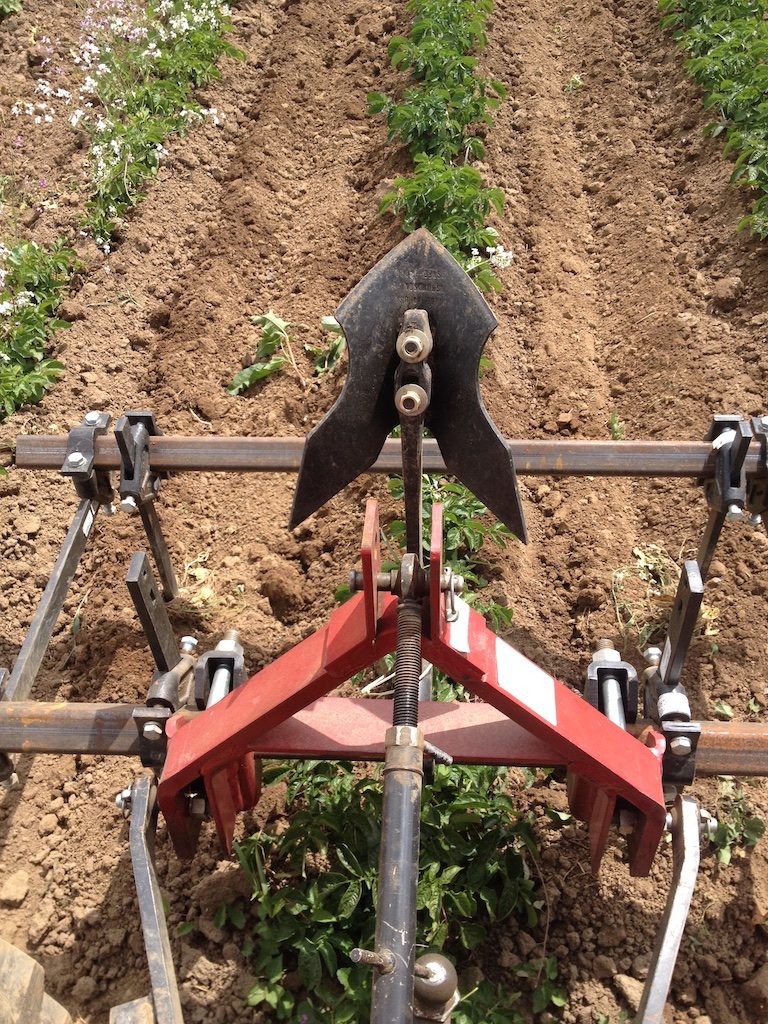
Lots of small farms I know, including many I’ve worked on, use a small tractor to mow and till, but do all of the planting and cultivation by hand. This is partly because on a really small scale setting up a tractor cultivator almost doesn’t make sense, and a lot of times it’s also because when you’ve never done cultivation with a tractor it can seem intimidating. Figuring out the equipment you need is intimidating, driving over your crops on a big tractor with pieces of steel that will potentially kill them is intimidating, and somewhat rightly so as the inevitable learning mistakes could be catastrophic.
The truth is you don’t need a special cultivating tractor to get started learning how to cultivate with a tractor, and you can set up a simple and effective tool bar for well under $1000, new, that can save much more than that in labor costs within the first year, even on operations that are just a few acres.
Before You Set Up a Tool Bar
There are a number of factors that make cultivating with a tractor -or by hand- much easier. Mechanical cultivation, whether with a hoe or a tractor, is much easier if your beds are relatively trash free: no clumps of un-decomopsed organic matter, old vines, or root stumps still hanging out. A relatively even soil texture, without big clods or rocks, and with a little soil moisture but relatively dry helps. An even, flat bed surface with plants in straight, even rows also makes things far easier. None of these things is particularly difficult, or what I’m going to cover in this post, but definitely keep them in mind.
My recommendation is to not get hung up on wanting to cultivate the space close to your plants when you first start, think about the big open spaces that can take up a lot of the field when plants are young, especially the pathways. The easiest place to cultivate, no matter how experienced you are, is between the rows, and especially in the pathways. This might only be 1/4 to 1/2 of the total area, but still, you’ve just cut your hand hoeing/weeding time and work potentially in half.
A Basic Tool Bar
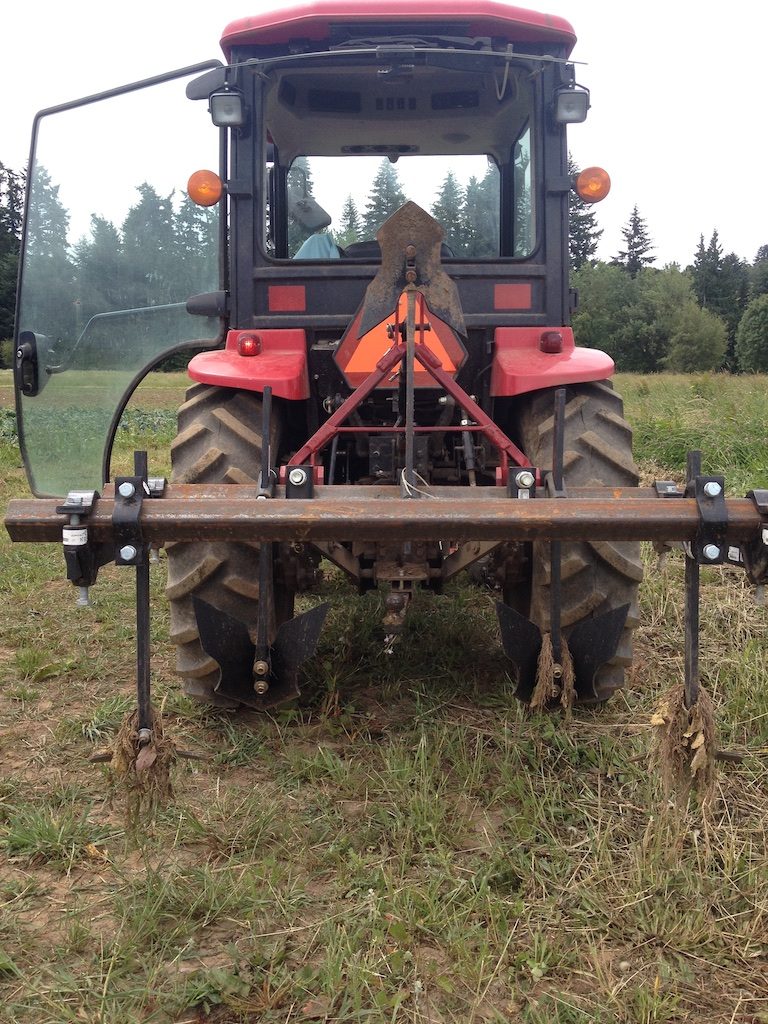
The two photos above (one at the start of the post and the one immediately above) show the same tool bar from two different angles, and I’ll include a photo below with yet another angle. On the outsides in the back are what I call sweeps and these are 9″ sweeps if I remember right. On the front bar there are two 12″ furrowers (people have different names for these same parts and there’s definitely variation in patterns from manufacturer to manufacturer). There is a third 9″ furrower that is mounted upside-down in the center. Mounting tools upside-down is a convenient way to store them completely out of the way when they’re not being used, especially if you might switch set ups out in the field.
The basic parts here are those “shoes,” meaning the furrowers and sweeps, the “shanks” that the shoes are attached to, the clamps that clamp the shanks to the tool bars. The bars themselves, which in this case are referred to as “diamond bar”, which is just square tube rotated 45 degrees. I’ve used four additional clamps with two straight shanks to offset the two tool bars and the front tool bar is mounted on a red A-Frame, which is the standard mount for a category 1 3-point hitch. The number after “category” refers to the sizes of the 3-point hitch, but category 1 is the most common size on small farms, sometimes category 2 when you get up into the 50+hp range, or category 0 if you have a really small tractor. If you have a really old tractor it probably has some other implement mounting system as the three point hitch wasn’t common until the 1960’s.
A strange note on diamond bar is that many clamps are made for 2 1/4″ diamond bar, but 2 1/4″ is not a standard size square tube that most steel yards carry so you usually are better off using 2″ for smaller tractors, and that usually works with most clamps. Some clamps work better with 2 1/2″ and that’s more appropriate for very heavy soil and wide tool bars. Most tool bars are hollow (a.k.a. square tube), with at least 1/4″ or 3/8″ wall, but when extra down pressure/weight is needed sometimes solid bars are used. They are extremely heavy and proportionally more expensive as plain steel is essentially a commodity sold by the pound.
There are lots of variations on all of these parts, especially the shanks, so you want to make sure when you’re buying the separate parts that they’re all compatible. Usually there’s quite a bit of cross compatibility. The shanks for the sweeps and furrowers have a special end for mounting the shoes on them and they need to be mounted with special bolts called “plow bolts.” These usually aren’t available at hardware stores anymore so you’ll need to get them from the same dealer you get the shoes and shanks from. Using a flat washer and and split washer on the back side of the shank with the nut for the plow bolt will keep the nut from vibrating loose.
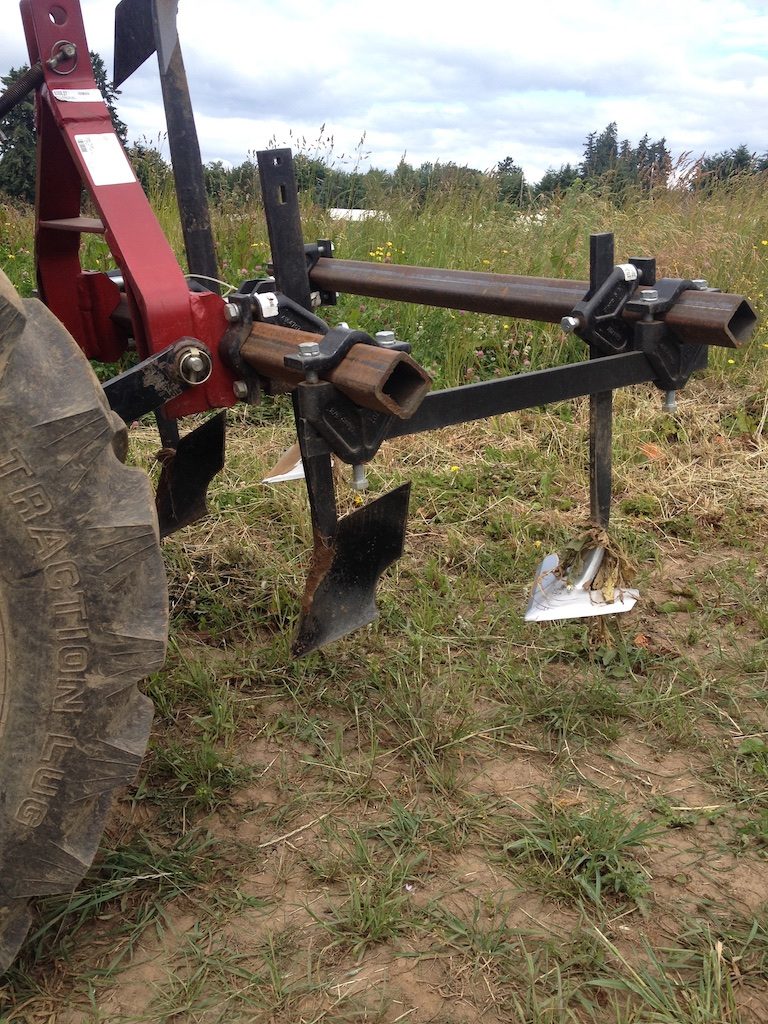
This particular set up was for hilling potatoes. The plants at this point are still short enough that they might touch the underside of the tractor, but they’re not going to be damaged by that contact. The two 12″ furrowers are pointed and have plow like wings that direct the soil that is dug by the points up and off to the sides. The sweeps are flatter and don’t have wings so while they still dig a bit and move some soil to the sides, most of the soil flows over the blade.
The way this tool bar is configured the furrowers are moving soil into the row of potatoes, hilling them up. This buries weeds in the row, and also cuts, or drags weeds out of the path of the furrower, killing those too. The furrowers are also moving soil into the pathway, but the sweeps are following so they cut and drag weeds out of that path, and help flatten the pathway back out.
As you can see there was trash in the field and it’s now hung up on the shanks. The chevron shape of the sweeps helps move most of the trash off to the side, but when it hits trash straight on it can get hung up. Depending on the speed and depth that the sweeps are run at, and the width of the sweep, they will have an effect on a swath of soil that is significantly wider than the sweep itself. I usually consider a 9″ sweep to cultivate a path about 12-4″ wide, and a 5″ sweep a path about 9″ wide. Going slower and shallower makes this narrower, faster and deeper makes it wider.
In general I find it better to use more smaller sweeps rather than fewer wider sweeps, but to offset them, alternating between the front and rear tool bars and to overlap them slightly to make sure you cover all of the ground. This offsetting front to rear leaves gaps in the front row and the back row and those gaps allow any trash or clods to flow around, while still killing all of the weeds. It also leaves a flatter surface, and is less stress on the individual shanks and shoes.
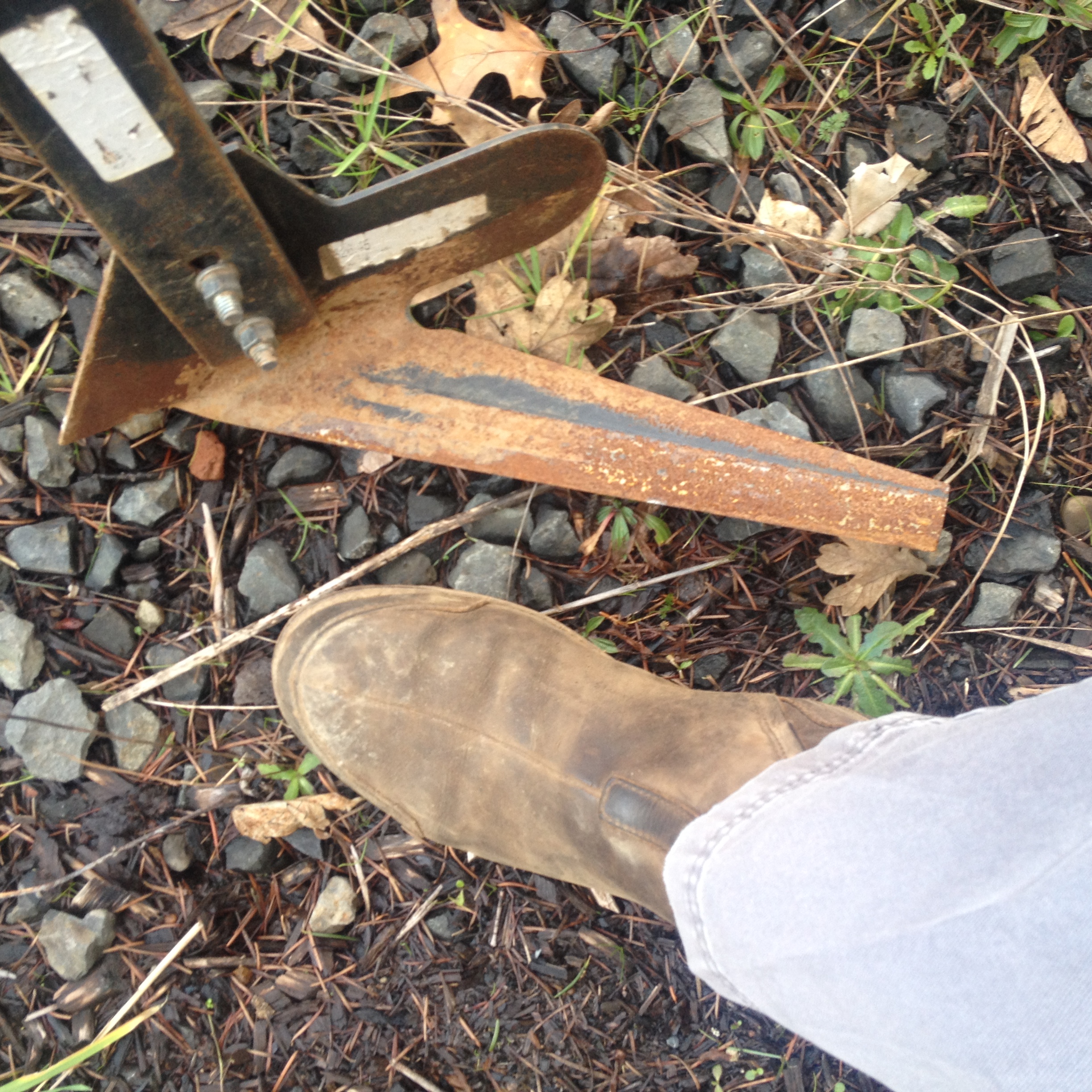
Another kind of tool that’s a little different than the standard sweeps and furrowers is a side knife, sometimes also called a beet knife. On the same tool bar shown above I can swap out the furrowers for side knives. If the knife is angled away from the row, with the shield running a few inches from the row of plants, it can be run just an inch or so under the surface and will move a little soil away from the plants, taking out weeds at the same time. For a single row of something like kale, or cabbage, or small tomato plants, this leaves a narrow strip of in line weeds just a few inches wide to clean up with a hoe. When the plants are a little larger I can turn the knives around so they move soil into the row, slightly burying the bases of the plants, and burying small in row weeds. Again, I run the sweeps in the pathways to keep those clean.
Making Adjustments
There are a number of ways to adjust the shanks, knives, and tool bars. I’ve talked a little about the position of the shanks and shoes on the tool bar, alternating between the front bar and rear bar, and overlapping the pathways a bit to take out weeds. To start, I usually leave a 5-7″ gap where the crop plants will pass through, or more for someone just starting out. The gap needs to be wide because it’s impossible to drive completely straight, although you will get better at this with time and dedicated cultivating tractors with belly mounted implements can help you get a little closer. The other reason the gap needs to be there is because the tool will throw a little soil into the gap, making it narrower than the way they tool is actually set.
Vertically I usually set the shanks about 3/4 of the way extended. Shorter is stronger and stiffer, but reduces the clearance for the plants passing under the tool bar. Fully extending the shanks is weaker and more flexible, risking bending the shanks and also reducing the ground clearance when the tool is lifted out of the ground.
You may notice that on the potato hilling tool bar the pathway sweeps are set a little deeper than the furrowers for hilling. This is because in this particular case the potatoes were already hilled a bit and so the path ways were lower than the shoulders of the bed where the furrowers were running. In general running the tool within the top two inches, is best.
On some sweeps and knives you can adjust the angle of attack, either setting the point so that it angles down slightly, or up slightly. Setting it with the point down will help it penetrate hard soil and dig in more, setting it flatter works better in loose soil where you can run the blade evenly shallow without the tool jumping out of the soil and skipping sections. You can also change this angle of attack by adjusting the top link on the 3 point, but you’ll have to make further adjustments to the length of the shanks between the front and rear tool bars to make sure all of the tools are running at the desired depths.
Driving Considerations
When you’re driving a tractor with the tool bar off of the rear 3 point when you start turning left the tool will actually initially move right, and vice-versa. Turning much with the tool in the ground is a bad idea as it puts lateral forces on the tools, and they aren’t designed to take those forces which means you’re likely to bend or break parts. Turning slightly to follow a row is inevitable, and the only trick here is to do it as subtly as possible, paying very close attention and making changes slowly. You will quickly learn how much better this works when the beds are formed and planted straight, without wiggles or curves.
You also need to pay constant attention to how deep the tool is running and make small adjustments with the 3 point lift arms. You can add gage wheels to set depth but this adds a layer of expense and complexity when setting up the tool and doesn’t completely eliminate the need to pay attention to what the tool is doing.
Start by driving very slowly while you get used to paying attention to both how straight you’re driving and how deep the tool is at any particular moment at the same time, and how to adjust those things on the fly. Eventually it will become ingrained and you’ll be able to drive faster as the micro-adjustments needed become second nature.
If you have 4 wheel drive on the tractor, especially if you’re on a slight side slope (side slopes make everything trickier), putting the tractor in 4 wheel drive can help you keep the tractor straighter, but take it off for the turn arounds at the ends of the rows.
Drip Tape Considerations
Aside from the need to make sure the tools clear the header at the beginning of beds, I’ve never had trouble cultivating with drip tape in place. Part of the trick is to make sure that the tape is straight before you start cultivating. The only other trick is to just pay attention and make sure you never snag it, and if you do you stop immediately and sort things out. For the most part the tools run under the tape and never touch it. (This is not true for rolling cultivators, which I’m intentionally not talking about here.)
Setting the Toolbar Up for Planting

By moving around a few of the pieces the same tool bar I showed above can be used to plant potatoes, and potentially other crops as well. The center furrower is now dropped to create a furrow for dropping the potato seed pieces into. The two larger furrowers are flipped because they’re not in use, and the sweeps are moved in tighter to full the furrow back in after the seed pieces have been put in the furrow.
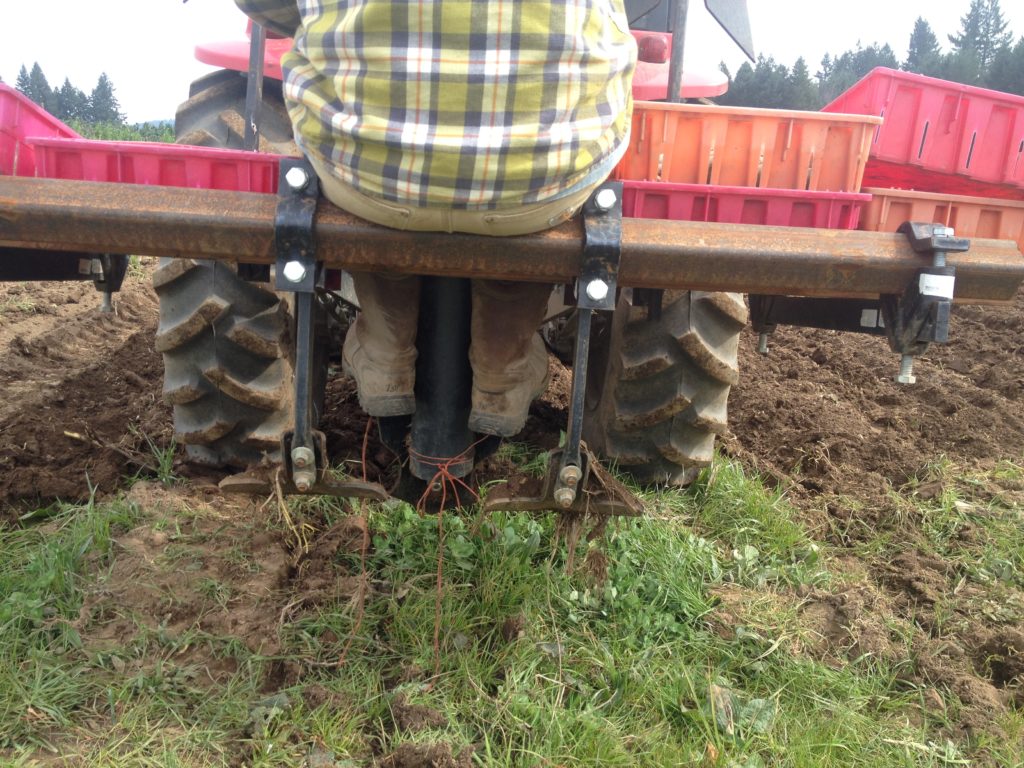
If you look closely at the photo you can see that a 4″ ABS pipe is tied to the back of the shank of the furrower. Seed pieces are dropped down the pipe and if you’re using 12″ spacing the lugs on the rear tires are conveniently 12″ apart, meaning you drop a piece every time a lug on the tire rolls past some set point on the tractor.
A board sits between the tool bars and acts both as a seat for the planter and a place to stack totes of potato seed pieces. You want to have excellent communication between the planter and the tractor driver to make sure that everything runs smoothly and safely.
For more ideas and lots of photos of cultivation tools I have a photo page with lots of captioned photos of tool bars, cultivation tractor set ups, and even hand tools here.